Контроль качества быстрого реагирования qrqc: Метод QRQC — Быстрое реагирование на проблемы качества. На основе опыта в лучшей команде Volvo. Объясняем на котах.
Метод QRQC — Быстрое реагирование на проблемы качества. На основе опыта в лучшей команде Volvo. Объясняем на котах.
Думаю, стоит сказать, что эта методика, в том виде, о котором пойдет речь, развивалась при мне. Я видел её начало, когда совсем зелёный пришёл на завод, видел, как она менялась и совершенствовалась, видел, как её результативно использовали для решения любой проблемы, которая возникала, и видел, как мы успешно перенесли её на другой завод бренда с другой спецификой, который запустили за полгода до моего ухода из компании. Да, что-то в ней мне не нравилось, что-то я обожал. Но здесь я сформулирую основные принципы, основанные на том, как это видел я и наша команда. Если вы грамотно и вдумчиво подойдёте к тому, что здесь написано, то получите мощный универсальный инструмент для решения практически любых проблем.
Заранее вас прошу не воспринимать этот материал, как лёгкий — нет ничего сложнее, чем правильно ответить на простой вопрос. На моей памяти много случаев, когда использовали отличные, удобные простые методики так, что это было больше похоже на форменное извращение.
QRQC (Quick Response Quality Control) является универсальным методом, позволяющим быстро реагировать на проблемы, возникающие как на производстве, так и на складе, а также при организации и продаже услуг. Этот метод позволяет докопаться до корневой причины и изменить процесс так, чтобы он работал без ошибок, в нужном вам формате.
Ключевой особенностью QRQC является то, что данный инструмент должен начинать работать сразу на месте обнаружения и возникновения ошибки. Проблема ни в коем случае не должна решаться умозрительно — только реальные вещи, реальные участники, реальные действия и реальные данные прямо на производственной линии.
QRQC = быстрое реагирование + предотвращение влияния на клиента + RCA
Вам необходимо определить лидера, отвечающего за правильность ведения QRQC, но важно, чтобы не он заполнял бланк QRQC, а ответственный за проблему, представляющий участок, на котором она возникла.
Участники:
Ответственный за проблему
Ответственный за ведение QRQC (обычно, сотрудник отдела качества или внешний тренер, умеющий правильно подойти к вопросу) — QRQC лидер
Представители всех вовлечённых в процесс команд (инженеры, технологи, логисты, операторы сборки и т.д.)
Итак.
QRQC [на котах]
На нашем странном заводе в процессе аудита готовой продукции, проводимым методом случайной выборки, обнаружена страшная проблема — кот не соответствует требуемым геометрическим параметрам.
Аудитор готовой продукции вызывает в аудиторское помещение сотрудника отдела качества и групп-лидера (бригадира) участка, где производится операция по откорму котов, так как предполагает, что проблема возникла именно там. Аудитор продолжает заниматься своей работой, сотрудник отделка качества фиксирует проблему и берёт на контроль, ответственный за проблему начинает QRQC.
Замечание: уверен, возникнут вопросы о том, почему проблемой не занимается отдел качества и т.п. В данном примере я говорю о настоящем отделе качества, который отвечает не за контроль, а за обеспечение качества и стабильности процессов. Отдел качества является драйвером решения проблем.
Шаг 1.
Зафиксировать проблему.
Проблема должна быть визуально понятна, лучше всего это покажут фотографии в формате Правильно (OK) — Неправильно (NOK), с пояснениями, лучше всего если это реальная фотография текущей проблемы, произошедшей только что. Если нет возможности сделать фотографию состояния ОК, то надо его максимально подробно описать, приложить чертежи, эскизы, всё, что даст понимание того, как должно быть правильно.
NOK — кот гораздно меньше установленных в технической документации геометрических параметров
OK — кот требуемого размера
Шаг 2
Анализ 5w2h
Это очень простой и понятный инструмент сбора первичных сведений о проблеме, позволяющий понять её суть, влияние на клиента и масштабы.
Только ключевые вопросы, ничего лишнего.
W | What | Что за проблема? Описание. |
W | Почему это проблема? Каково влияние на клиента? | |
W | Who | Кто обнаружил проблему? |
W | Where | Где она была обнаружена (место) |
W | When | Когда она была обнаружена (дата, время) |
H | How | Как проблема была обнаружена? |
H | How much | Сколько раз была обнаружена проблема? |
В случае с котом всё выглядело так:
What | Геометрические параметры кота не соответствуют требованиям технической документации. |
Why | Кот меньшего размера самостоятельно помещается во все незначительные отверстия, что может привести к недопустимому нарушению целостности кота и выходу его из строя – замена кота по гарантии.![]() |
Who | Аудитор качества готовой продукции Котеев О.Т. |
Where | Выборочный аудит качества готовой продукции. |
When | 1 апреля |
How | В процессе проверки кота непроходными калибрами |
How much | 8 за последнюю неделю |
Шаг 3
График возникновения проблемы
На графике отображаются все известные случаи. Если выяснится, что подобная проблема встречалась раньше, то она отображается в начале графика, даже если это было год назад.
График даёт визуальное представление о частоте возникновения проблемы и иногда позволяет сделать выводы о зависимости возникновения проблемы во времени
Шаг 4
Место возникновения и обнаружения проблемы в потоке
Определите место обнаружения проблемы в потоке и место, где проблема могла возникнуть. В нашем случае дефектного кота обнаружил аудитор, а возник он, кажется, на этапе откорма.
Поток рисуется связанными блоками, где каждый блок либо этап, либо отображает часть процесса, которую мы не рассматриваем, т.е. например, сильно в начале процесса сборки — в этом случае в блоке ставится многоточие. Придумайте, какие символы вы будете применять для обозначения этапа процесса, на котором проблема обнаружена (например, глаз или галочка) и этапа, на котором проблема возникла или предположительно возникла (прицел, молния, восклицательный знак).
Шаг 5
Предупреждающие действия
Один из самых важных шагов.
Иногда, если проблема имеет очень серьёзные предполагаемые последствия, начинают с этого шага, чтобы, руководствуясь даже минимумом имеющейся информации, предотвратить негативное влияние на клиента. Определите правила, когда вы начинаете с этого шага. Это важно.
Когда суть проблемы ясна, необходимо определить предупреждающие действия – действия, которые не должны допустить попадания несоответствующей продукции или услуги как к финальному клиенту, так и на следующий этап процесса от предполагаемого места возникновения.
Основная задача – защита клиента.
Для начала этапа планирования действий и дальнейшего анализа необходимо собрать кросс-функциональную команду из представителей различных подразделений компании, вовлечённых в производство/предоставление услуги.
Ключевой фактор — скорость принятия решения и их нацеленность на результат.
1.Опишите действие
2.Назначьте ответственного за выполнение, это должен быть один из присутствующих при анализе проблемы – ответственный может быть только один, где два и больше – там нет ответственных
3.Определите дату готовности
Действие | Ответственный | Дата | Статус | |
1 | Обеспечить сплошной контроль калибром перед складом готовой продукции | Котов. К.К | 1 апреля | ок |
2 | Проверить склад готовой продукции начиная с последней партии, размер проверки — партия следующей отгрузки + одна партия в случае обнаружения несоответствия в предыдущей | Котин.![]() | 1 апреля | |
3 | Проверка выходящего кота с процесса откорма на соответствие требованиям стандарта | Иван Иваныч | 1 апреля | |
4 | Определить модель кота во всех случаях обнаруженных несоответствий | Василий Петрович | 1 апреля |
Важно понимать, что не всегда можно обеспечить сплошной контроль и следует воспользоваться выборками продукции.
Также нет смысла делать сразу полную проверку склада, может проблема только с рыжими котами, тогда контроль будет упрощён, время и деньги сэкономлены.
Для каждого действия задавайте себе вопрос – поможет ли это действие здесь и сейчас не допустить несоответствие на следующем этапе процесса и защитить клиента. Если нет, то скорее всего это долгосрочное корректирующее действие.
Шаг 6
5Why
Думаете Нет ничего проще, чем задать пять вопросов почему? Ещё чего! Об этом я и писал в начале.
Стоит провести 5 Почему дважды – по причине возникновения проблемы и по причине, по которой её не обнаружили.
Проблема | Геометрические параметры кота не соответствуют требованиям конструкторской документации. |
Почему? | Кот меньше требуемого размера |
Почему? | Процесс откорма и доведения кота до требуемых параметров выпустил ненадлежащего кота |
Почему? | Кот был выпущен раньше времени до достижения необходимых параметров |
Почему? | В процесс не заложен контроль времени откорма кота |
Почему? | Требования контроля времени не предъявлялись при разработке процесса |
Естественно, тут всё притянуто за уши (кота), такого процесса нет. Но необходимо понять, что задавая вопросы вы должны найти корневую причину, в этом случае это отсутствие предъявленных требований при разработке процесса.
Скорее всего, задавая вопросы, в 95% случаев вы будете находить в роли причины человеческую ошибку – ошибка оператора/сотрудника и т.п. , но на самом деле человеческая ошибка это 5% случаев, а в 95% это проблемы управления процессом, например, отсутствие встроенного качества, допускающее переход ошибки на следующий этап.
А теперь посмотрим почему кота не нашли сразу.
Проблема | Геометрические параметры кота не соответствуют требованиям технической документации. Дефектный кот не обнаружен до передачи на склад готовой продукции |
Почему? | Тесты не обнаружили ошибку |
Почему? | Тесты обнаруживают только функциональные ошибки. |
Почему? | Контроль геометрии в тесты не заложен так как считается, что неоткормленный кот не выпускается |
Почему? | При проектировании производства подобные возможные ошикби не были учтены |
Почему? | На других производствах подобные ошибки никогда не возникали |
Тут абсолютно та же механика, только необходимо понять, почему процесс позволяет выпускать несоответствующую продукцию, и это никак не обнаруживается. Это может быть намёком на место, где в процессе может быть встроена poka-yoke.
Шаг 7
Корректирующие действия
Также, как и с 5why их можно разделить на две части – устранение корневой причины и встраивание контроля.
Но надо понимать, что контроль не создаёт ценности, и его надо по возможности минимизировать.
Корректирующие действия планируются абсолютно также, как и предупреждающие действия. Один в один.
Шаг 8
Контроль
Контроль проводится для проверки результативности запланированных корректирующих действий.
И опять всё то же самое:
- Описание проверки
- Ответственный
- Дата начала проверки
- Дата окончания проверки
- Статус – Ok/Nok
Если проверка показала, что проблема не устранена, то причина была выявлена неверно – необходим новый анализ корневых причин с учётом всех новых известных данных.
Если вы посмотрите внимательно, то вы обнаружите здесь заложенный PDCA цикл — всё по лучшим практикам.
Со своей стороны советую вам сделать стандартный бланк на большом листе, например, А2, который вы будете вешать на досках или флипчартах и заполнять, приклеивая фотографии и занося данные прямо на месте. Хранится они будут у вас там же, на участке, где была обнаружена проблема, а фотографии заполненных бланков в высоком разрешении по окончании расследования вы будете хранить где-то в электронных базах данных.
Немного о роли QRQC лидера
Этот человек должен очень хорошо знать всё, что происходит у вас на заводе, уметь найти логические нестыковки в рассуждениях, правильно применять все простые и непростые инструменты качества. Он не должен быть заинтересованной стороной, потому что часто те, кто отвечает за проблему пытаются увести в сторону, доказать, что это не они и не потому, что делают это специально, а потому, что верят в то, что не могли так ошибиться (ага! Сейчас!). Лидер направляет расследование и корректирует действия, обсуждая их с участниками для правильного и логичного разрешения ситуации.
Если вы прибегаете к помощи внешних консультантво, выстраивая систему обеспечения качества, внедряя различные методики, то QRQC лидер не будет знаком с вашим предприятием так, как знакомы вы, но он научит вас правильно задавать вопросы и не уходить в сторону.
Поменьше вам проблем!
С уважением,
Quorace.com
Вы можете скачать готовый бланк QRQC у нас на сайте: Бланк QRQC
8D / QRQC Анализ – Тренинг SNECI
АНАЛИЗ КОРНЕВЫХ ПРИЧИН: 8D / QRQC
Стандарты и инструменты качества – QTS08 – Внутреннее и межфирменное
Данный тренинг позволит участникам развить их навыки и углубить знания методов решения проблем посредством процесса 8D/QRQC и применить их на практике с помощью упражнений.
Этот тренинг сертифицирован FIEV.
1 день Все помещения SNECI
Содержание обучения
1. Методы решения проблем
2. Стадии анализа 8D/QRQC
3. Определение команды по решению проблем
4. Изложение проблемы: 5W2H, рецидивы
5. Поиск потенциальных исходных причин
— Анализ дерева неисправностей, диаграмма Исикавы, 5 почему
6. Определить причину с помощью доказательств
7. Определить корректирующие решения
8. Контроль эффективности действий
9. Определение превентивных мер
10. Разбор примеров 8D / QRQC
Оценка результата
Приобретенные знания оцениваются и проверяются в конце обучения с помощью теста. Этот тест проверяется участниками вместе с преподавателем.
Участники получают сертификат об участии в тренинге.
Методика обучения
Тренинг позволит вам понять процесс и методологию решения задач в автомобильной отрасли с помощью упражнений для выявления и устранения коренных причин проблемы.
Проводится тест для проверки полученных знаний. Участникам выдается печатное Руководство и оказывается конкретная поддержка.
Опция: совещание
Дополнительно к данной сессии тренинга и в случае, если обучение проводится на предприятии, преподаватель SNECI может выполнить вместе с Вашими командами 8D/QRQC совещание по одной из внутренних проблем.
Предназначен для
- Менеджер по качеству
- Менеджер по производству
- Инженер / технический специалист по качеству проекта
- Любое лицо вовлеченное в группы по решению проблем
Цели и результаты
- Освоить методику по решению проблем
- Уметь проводить совещания по решению проблем
- Знать различные инструменты по решению проблем
- Внедрить процедуру отчета о решении проблемы в соответствии с методологией QRQC/8D
- Создать команду быстрого реагирования
- Разработать действия для защиты клиента
- Определить и подтвердить исходные причины несоответствий
- Разработать корректирующие и предупреждающие действия, чтобы избежать повторения
Требования
Опыт работы в автопроме.
Ваш тренер
Тренинг проводится специалистом по качеству с многолетним опытом работы в автопроме.
Training dates
- 18/03/2021
- 17/06/2021
- 09/12/2021
Внедрение процедур быстрого реагирования QRQC
Специалисты подразделений применяют статистические методы, которые включают в себя следующие инструменты качества: Диаграмма Парето, Контрольный листок, Контрольные карты Шухарта, Диаграмма Исикавы, Диаграмма рассеивания, Стратификация, Гистограмма. Эти методы позволяет без потерь времени провести статистический анализ и составить отчет для быстрого реагирования на проблемы в области качества.
Диаграмма Парето распределяет отдельные области по значимости или важности и позволяет выявить и в первую очередь устранить те причины, которые вызывают наибольшее количество несоответствий (80 %).
Для построения диаграммы Парето исходные данные представляют в виде таблицы, в первой графе которой указывают анализируемые факторы, во второй – абсолютные данные, характеризующие число случаев обнаружения анализируемых факторов в рассматриваемый период, в третьей – суммарное число факторов по видам, в четвертой – их процентное соотношение, в пятой – кумулятивный (накопленный) процент случаев обнаружения факторов.
Контрольный листок – инструмент, позволяющий облегчить задачу контроля протекающих процессов и предоставить различного рода факты для анализа, корректировки и улучшения качества процессов.
Контрольные карты Шухарта (КК) позволяют контролировать текущие рабочие характеристики процесса и показывают отклонения от стандарта, целевого или среднего значения, а также уровень статистического контроля процесса в течение определенного времени. В общем случае КК имеют вид, представленный на рисунке 11, и отображают характер изменения показателя качества во времени.
Рис. 11 Общий вид контрольной карты
Диаграмма Исикавы (причинно-следственная диаграмма) – инструмент, позволяющий выявить и систематизировать наиболее существенные факторы (потенциальные причины), влияющие на конечный результат (следствие). Многие потенциальные причины сводятся в главные категории и подкатегории так, что обнаруживается сходство со скелетом рыбы.
Процесс построения диаграммы Исикавы начинают с описания выбранного показателя качества или связанной с ним проблемы, а именно: в чем ее особенности, где она возникает, когда проявляется и как далеко распространяется.
Диаграмма рассеяния (разброса)представляет собой графическое отображение взаимосвязи между различными видами данных, описывающих рассматриваемый объект.Она используется для качественной оценки взаимосвязи между данными.
Диаграмма рассеяния применяется при анализе взаимосвязи между входами и выходами процесса, между параметрами процесса и характеристиками продукции, для установления причинно-следственной зависимости (рисунок 12).
Рис. 12 Пример диаграммы рассеяния (разброса).
Расслоение (стратификация) –это группировка данных в зависимости от источников и условий их получения. Расслоение помогает выяснить причину появления дефекта, если обнаруживается различие в данных между «слоями» (стратами).
Гистограмма– столбиковые диаграммы, показывающие количественную оценку частоты попадания зарегистрированных событий в установленные интервалы.По виду гистограммы можно анализировать форму и параметры распределения, однородность зарегистрированных данных. Вид гистограммы может указать на наличие нескольких источников данных и целесообразность расслоения данных по источникам.
Гистограммы используются для представления структуры и характера изменчивости данных, которые трудно заметить при их табличном представлении (рисунок 12).
Рис. 12 Пример использования гистограмм
Статистические методы применяются автономно, поэтому следует внедрить метод быстрого реагирования QRQC, который так же будет включать в себя статистические инструменты качества, а также другие методы и инструменты повышения качества продукции.
Семинар Командные методики быстрого решения проблем: SIXSIGMA, 8D, QPQC 2021
Инициаторы, триггеры преобразований (изменений) системы управления.
- C чего начать оптимизацию процессов. Опережающие признаки необходимости оптимизации.
- Источники проблем (несоответствий).
Классический вариант решения проблем (определение, диагностика, формулирование, определение ограничений, перебор альтернатив, определение критерия выбора решения, выбор оптимального решения).
Реактивные и про активные методики решения проблем.
Методики быстрого решения проблем.
Командные методики решения проблем (несоответствий).
- Задачи, принципы организации командных методик.
- Методика PDCA.
- Методика Кайдзен.
- Методика QRQC(Quick Response Quality Control — быстрое реагирование на проблемы.
- Примеры применения командных методик.
Основные принципы командной методики решения проблем 8 D.
- Цели, задачи, для решения которых предназначена методика 8D.
- Область применения методики 8D.
- Краткое содержание методики 8 D.
- D0 – Определение проблемы и разработка плана.
- D1 – Формирование команды.
- D2 – Описание проблемы.
- D3 – Сдерживание проблемы.
- D4 – Анализ проблемы.
- D5 – Разработка корректирующих мероприятий.
- D6 – Внедрение и валидация корректирующих действий.
- D7 – Разработка предупреждающих действий.
- D8 – Закрытие мини проекта 8D.
- Анализ преимуществ и недостатков методики 8 D.
Практикум: Примеры применения методики 8 D.
Концепция повышения операционной эффективности Six Sigma.
- Принципы, основные отличия концепции Six Sigma.
- Методология DMAIC.
- Возможности, области применения методологии DMAIC
- Стандартная последовательность этапов в проекте DMAIC.
- Define (определяй). Определение проблемы, процесса, требований клиентов.
- Применение SIPOC для процессов верхнего уровня.
- Определение показателей критичных для качества (VOC, CTQ).
- Устав проекта.
- Коммуникации проекта.
- Риски проекта.
- Команда проекта. Мотивация участников проекта.
- Управление проектом. Технология Scrum.
Практикум: Примеры устава и рисков проекта.
Measure (измеряй). Примеры инструментов измерения метрик.
- Моделирования процессов.
- Измерение метрик процессов.
Практикум: Организация измерения метрик процессов.
Analyze (анализируй). Рассмотрение инструментов анализа проблемных областей.
- Диаграмма Исикавы, Пять почему, анализ Парето, анализ FMEA.
- Анализ процессов с помощью различных нотаций. Применение SIPOC.
- Оптимизация затрат, оптимизация процессов, минимизация потерь – в чем разница этих подходов?
Практикум: Анализ использования различных нотаций в целях оптимизации процессов.
Практикум: Анализ статистических данных. Применение статистических критериев для проверки гипотез.
Improve (совершенствуй).
Практикум: Примеры вовлечения персонала в Российских и зарубежных компаниях в процесс совершенствования (улучшения) процессов.
- Применение технологий бережливое производство в управленческих и операционных процессах.
- Бережливый офис, это там где на всем экономят или что то другое?
- Виды потерь.
Практикум: Анализ потерь в подразделениях. Коллективное обсуждение мер по снижению потерь.
Control (проверяй).
- Разработка плана контроля.
- Документирование действий по процессу.
Практикум: Примеры использования методики 8D при обнаружении проблем и несоответствий.
Практикум: Рассмотрение действий проектной команд.
Руководителей и топ-менеджеров компаний, для проектных менеджеров и специалистов по постановке и оптимизации бизнес-процессов.
Семинар
Возможно заказать в корпоративном формате (обучение не менее 10 сотрудников по программе, адаптированной под потребности компании).
Методический материал, обеды, кофе-паузы.
Сертификат об участии в семинаре.
Успех всегда приносит популярность и внимание. Особенно если речь идет об успехе в бизнесе. Компании, достигшие успеха, оказываются в центре внимания. Такие компании становятся “популярными”, их успех рассматривают, обсуждают, описывают в книгах. Все это делается для изучения принципов успешного менеджмента с целью их применения в других организациях. В цикле статей “Опыт Valeo”, мы рассмотрим возможности принципа San Gen Shugi и методики QRQC как ключевых факторов успеха компании и достижения высоких показателей качества продукции. Визитная карточка компании История компании началась с 1923г., когда было основано первое предприятие по производству автомобильных фар в Сейнт-Оуене, Франция. Сегодня Valeo – один из ведущих в мире производителей комплектующих деталей для автомобилей. Штат сотрудников насчитывает более 70 000 человек. Компания владеет 136 заводами в 26 странах. Продукция Valeo используется такими производителями как: VW, Nissan, Renault, BMW, Ford, Chrysler, Toyota, Mercedes и т.д. Производство и инновации Valeo сфокусированы на трех основных направлениях:
Высокое качество продукции Valeo достигается, в первую очередь, благодаря культуре компании, основанной на 5 основополагающих:
В рамках осуществления цикла Деминга компания регулярно проводит аудит V5000 и внедряет методологию быстрой реакции на проблемы качества – QRQC во всех сферах деятельности. В основу стратегии управления качеством продукции компания вложила принцип San Gen Shugi: принцип ориентации на реальные показатели. Подход Valeo Уровень качества продукции можно назвать визитной карточкой организации, реквизитом. Целью создания качественной продукции и поддержанием качества является удовлетворенность потребителя/заказчика. Ориентация на потребителя – это основа успешного менеджмента организации. Это также одно из требований международных стандартов качества ISO 9001 и ISO/TS 16949. Обратная сторона качества продукции – уровень брака. Достичь наивысшего качества продукции можно лишь снизив количество дефектов продукции до 0. 0 ppm – вот цель любой уважающей себя организации, ориентированной на достижение удовлетворенности заказчика и нацеленной на успех в будущем. Все эти утверждения отнюдь не новы. Это то, о чем твердят уже много лет ведущие специалисты в области обеспечения качества. Это основы многих методик, принципов и инструментов качества. К сожалению, многие (читай все) организации далеки от этих показателей. Среднестатистическая организация автопрома работает с уровнем отказов около 100 000 ppm, что соответствует нескольким десяткам в смену. Затраты на повышение качества и устранение дефектов составляют колоссальные убытки для предприятия, его работников и общества в целом. И что хуже всего, все принимаемые меры не обеспечивают выпуск 100% качественной продукции, а соответственно не обеспечивают удовлетворенности потребителя/заказчика. Итак, почему? Почему имея такое количество инструментов качества и методик его повышения, разрабатывая проекты и валидируя процессы, зная о требованиях заказчика и видя желаемые целевые значения мы все еще терпим неудачи в попытках достичь уровня брака равного 0? Есть три основные причины:
Вернемся к основам: когда появляется проблема, необходимо видеть ее своими глазами и решать на месте. Проблемы качества не могут быть решены “в голове” или комнате совещаний. Подход San Gen Shugi, в первую очередь, меняет культуру организации. Основная цель – обеспечить немедленный анализ и устранение проблем качества, обеспечить быструю реакцию на возникшую проблему. Как только возникает проблема, наступает время ее решать. Этот принцип Valeo применяет везде – в обеспечении качества, разработке новых проектов, работе с поставщиками и т.д. Методика повышения качества, применяемая Valeo, основанная на принципе San Gen Shugi называется Quick Response Quality Control (Быстрая реакция на проблемы качества продукции). QRQC – это мощный инструмент улучшения и быстрого решения проблем. После внедрения QRQC во всех сферах деятельности, компания Valeo рапортовала о снижении уровня брака на 92% в течение 5 лет. Принцип San Gen Shugi Как быстро следует решать проблему? Само собой, что чем быстрее, тем лучше. Такой ответ сам напрашивается, но разве он несет хоть какую-то полезную информацию? Разве в нем присутствует указание целевого периода времени для решения проблемы? Вот и получается, что проблемы качества продукции постоянно находятся на стадии решения. И, чаще всего, не находят логического решения в связи с потерей актуальности или, что очень часто бывает, потерей заказчика. В некоторых компаниях жестко установлены временные рамки решения проблемы. Взять, к примеру, метод 8D, целевое значение закрытия протокола составляет 24-30 дней. Казалось бы – не плохо, но в компании Valeo совсем другого мнения. San Gen Shugi – это культура и основной принцип обеспечения качества компании Valeo.
San Gen Shugi также адресует проблему к временному показателю. Решение проблемы длится в реальном времени и сокращение временного интервала положительно сказывается на результативности работы предприятия. Как только возникла проблема, следует немедленно перейти к ее анализу и решению. Вместо траты недель на получение результатов следует сфокусироваться на днях, вместо дней – на часах. Следуя принципу San Gen Shugi и внося ежедневные улучшения в процессы, осуществляется цикл постоянного улучшения (PDCA). Приводя в действие небольшие локальные изменения с целью повышения качества, успешно внедряется подход постоянного улучшения Kaizen. San Gen Shugi vs. PDCA Международный стандарт качества автомобильной промышленности ISO/TS 16949 определяет концепцию PDCA как метод постоянного улучшения. Принцип San Gen Shugi отнюдь не идет в разрез с циклом постоянного улучшения. Напротив, их взаимосвязь может быть даже глубже, чем кажется с первого взгляда. Рассмотрим более подробно интеграцию принципов менеджмента Valeo и цикла постоянного улучшения:
Компания Valeo успешно реализует принцип San Gen Shugi в рамках осуществления цикла постоянного улучшения. Основы QRQC По аналогии с циклом PDCA, действие QRQC можно представить в виде следующего цикла: Сфокусируемся на качестве продукции:
Под участком следует понимать отдельную автономную зону или подразделение. На первом уровне QRQC, анализ и решение проблемы проводится операторами линии без вовлечения инженерного состава. Для успешной реализации QRQC, Valeo внедряет данную стратегию не только на разных уровнях, но и во всех сферах деятельности: начиная от работы с поставщиками и заканчивая гарантийным ремонтом. Основное что следует понять о QRQC – что это не панацея от всех проблем и не методика улучшения конкретного процесса.
|
DPD внедряет Lean
Инициатива поможет оптимизировать процесс работы и максимально уменьшить потери
Lean (или бережливое производство) – это комплекс бизнес-методов, направленных на устранение потерь c целью создания и увеличения ценности для конечного потребителя.
Пилот состоялся осенью прошлого года на территории сортировочного центра в Домодедово. В рабочую группу вошли сотрудники производства, закупок, продаж, маркетинга, IT и HR. На протяжении трех дней участники исследовали отдельные составляющие процесса работы, используя лишь некоторые из инструментов бережливого производства. Были рассмотрены процессы разгрузки, укладки посылок на линию, обработки негабаритных отправлений.
За это время было выдвинуто более сотни предложений по улучшению процессов. Вместе с сотрудниками терминала рабочая группа вносила первые корректировки. Изменения коснулись эргономики оклейки грузов на линии, оптимизации подъезда транспорта к сортировочному центру, способов замера габаритов посылок и разметки на терминале. Те потери, которые не удалось устранить, были внесены в базу для дальнейшего анализа и модификации.
«C февраля мы начали процесс полноценного перехода на Lean философию, результаты использования которой, надеемся, не только сделают процессы эффективнее и удобнее для сотрудников, но и порадуют наших клиентов и получателей. Сейчас мы внедряем изменения на хабе в Домодедово, в будущем планируем распространить практику на другие терминалы Москвы и области, а затем и на региональные отделения. В перспективе будем использовать инструменты Lean не только в сортировке, – говорит Сергей Ступарь, начальник отдела стратегических проектов DPD в России. – Одной из основных задач рабочей группы мы считаем вовлечение максимального количества персонала в процесс постоянного улучшения».
Lean рассматривает операции не как совокупность отдельных процессов, а как единый поток создания ценности. Необходимо видеть и понимать эти ценности, а также непрерывно устранять потери.
Простые потери можно решать с помощью инструмента «Быстрые улучшения», для более сложных потерь существует QRQC (Quick Response Quality Contro
Подход Lean был разработан в компании Toyota, он помог ей стать одним из ведущих мировых автопроизводителей. Сейчас методику бережливого производства успешно применяют по всему миру на предприятиях совершенно разных отраслей.
Стратегия лидера | Время ОВК
№ 2 (сентябрь) 2016
Инвестиции в качественные характеристики продукции – это стратегия лидера.
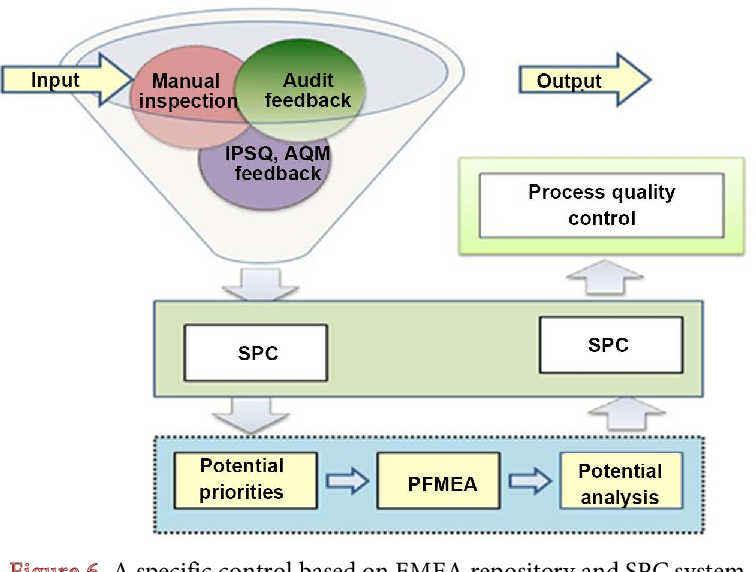
Елена Белянина,
директор по качеству НПК ОВК
Для Вас как руководителя что значит качество? Как Вы понимаете этот термин и как соотносите его с работой?
Качество – это комплексное понятие. Возьмем любой товар, произведенный руками человека. Нетрудно проследить, как в ходе технического прогресса он постепенно обретал те полезные потребительские свойства, которые мы так ценим. Это и есть в широком смысле качество, заложенное в товар на стадии проекта и даже раньше – в саму идею создать его и предложить рынку.
Качество в первую очередь символизирует развитие, прогресс, являющиеся результатом напряженной творческой работы множества людей. Едва ли можно рассчитывать на успех, производя добротную, но морально устаревшую технику, равно как и самый инновационный продукт, если не обеспечен необходимый уровень его эксплуатационной надежности. Напротив, если произведенный товар содержит все необходимые составляющие качества, перед ним падут любые преграды на пути к потребителю. В этом смысле качество – самый неотразимый аргумент в продвижении товара.
Часто приходится слышать мнение, что качество – это некий компромисс между затратами, которые мы можем себе позволить на поддержание того или иного уровня производства, и преимуществами, которые этот уровень обеспечит выпускаемому товару. Возможно, такой подход – взвешивать плюсы и минусы – пригоден для компании, ставящей задачу лишь сохранить завоеванный ранее кусочек рыночного пирога, пережить трудные времена.
«Объединенная Вагонная Компания» – молодая, энергично растущая организация, быстро осваивает новые горизонты и направления бизнеса. Для компании, находящейся на этой стадии развития, качество выпускаемой продукции и сервиса – это нечто большее, чем просто компромисс или экономический расчет. Мы стараемся не только соответствовать установленным требованиям, но и повышать их, стремимся предложить клиенту то, что выше его ожиданий.
Вопросы обеспечения качества должны превалировать в жизни производства, быть идеологией бизнеса. Кстати, это вовсе не означает непременное наращивание затрат, а в первую очередь требует преодоления стереотипов в сознании людей.
Интересно, что Эдвард Деминг, архитектор послевоенной технологической революции в Японии, всегда категорически настаивал на участии самых высоких руководителей корпораций в построении системы качества. Он понимал, что изменить отношение работников к вопросам качества можно, лишь фокусируя внимание на эту задачу всех звеньев компании – от управленческих до исполнительских.
Контроль микроструктуры металлургических образцов производится на инвертированном металлографическом микроскопе Olympus (Япония). |
Кто сегодня является главным контролером качества, кто, как говорится, «заказывает музыку»?
Наша отрасль имеет свою специфику, связанную с обеспечением безопасности. В ней действует целая система стандартов, нормативных документов, практически весь жизненный цикл продукта детально зарегулирован. А чем технологичнее продукт, тем требования жестче и строже.
То, что остается за пределами стандартов, производитель регламентирует техническими условиями. У каждого производителя они свои, отличные от других, в конечном итоге это оказывает влияние на потребительские свойства продукции и является серьезным конкурентным преимуществом.
Это, если так можно сказать, законодательный уровень управления качеством. Собственно контроль осуществляется на исполнительном уровне. Для этого созданы заводские дирекции по качеству и центры, осуществляющие независимую приемку продукции. Общая координация работы этого комплекса, состоящего из служб технического контроля, лабораторий, метрологических служб, осуществляется дирекцией по качеству «Объединенной Вагонной Компании».
Кто является инициатором изменения качественных параметров подвижного состава? Производитель или клиент?
Это дорога с двусторонним движением. С одной стороны, тот или иной уровень качества закладывается на стадии разработки, идеи создания продукта. То есть базовые решения формируются еще на этапе проектирования. С другой стороны, роль маркетолога очень важна. Ведь прежде чем создать тот или иной продукт, анализируются рыночные ниши, клиентский интерес, актуальные потребности.
Следующий уровень работы над качеством – проработка технологии изготовления. Причем начинается он еще до производства, что называется, «на входе», в тот момент, когда к нам поступают комплектующие, узлы и материалы.
Контроль механических свойств металлических образцов производится на универсальной испытательной машине Shimadzu (Япония). |
То есть у ворот предприятия их встречают суровые мужчины с рулетками и начинают контролировать?
Нет, на входном контроле их встречают, как правило, красивые девушки из службы входного контроля ТВСЗ. В контроле качества комплектующих участвуют разные подразделения. Например, центральная заводская лаборатория проверяет марку материала, его химический состав и механические свойства. Соответствие конструкционным требованиям оценивает контролер. Тут одними рулетками не справиться. Необходимо современное измерительное, испытательное и аналитическое оборудование и высокая квалификация персонала.
Далее полученные результаты необходимо обработать и передать в производство. Сейчас в нашей компании внедряется система входного контроля «Сокол» – мощный информационный ресурс, позволяющий все данные входного контроля, каждый инструментально полученный показатель вносить в общую базу, доступную заинтересованным пользователям. Такого ресурса по уровню интеграции и сервисов нет ни у кого – мы здесь передовики, вне всяких сомнений.
Подобный подход при производстве подвижного состава – это норма или исключение?
Для каких-то компаний входной контроль – процедура формальная. У других для этого банально не хватает ресурсов. Мы же, инвестируя в качество, считаем это своим конкурентным преимуществом. Благодаря выстроенной системе входного контроля наше предприятие работает только с качественными комплектующими и материалами.
Как строятся Ваши взаимоотношения с партнерами, если они поставляют некачественную продукцию?
Вопрос минимизации рисков для нас принципиален. Мы стремимся к тому, чтобы вероятность попадания на предприятие некачественных комплектующих была нулевая.
Еще одна важная функция, стоящая перед нами, – обеспечение обратной связи с поставщиком. На наших вагоностроительных предприятиях действует стандарт, который регулирует как раз процесс одобрения поставщика. Существует категорийность поставщиков: «одобренные», «сомнительные» и «красные», то есть те, с которыми работать можно только при 100%-ном сплошном входном контроле. Если появляется альтернатива такому поставщику, мы отказываемся от его услуг. Нам выгодно работать с теми, чья продукция не вызывает нареканий. Если поставщик производит продукцию стабильно высокого уровня, то уровень контроля мы понижаем до выборочного или можем вообще перейти на документарный. Такая ситуация для нас самая благоприятная. Нет необходимости тратить дополнительные силы и средства на контрольные мероприятия.
Как дальше контролируется производственный процесс?
Дальше идет пооперационный контроль, когда во время создания продукта контролируется правильность выполнения всех производственных операций. Это функция служб технического контроля в производственных подразделениях. Задача контролера – оценить все параметры производимой продукции на конкретном участке и сверить их с нормативными документами. Если он фиксирует нарушения, его обязанность – известить собственного руководителя и сотрудника, отвечающего за работу участка. В зависимости от сложности выявленной проблемы к ее решению оперативно привлекаются ответственные специалисты.
По каждому отклонению производится тщательная проработка мер, направленных на исключение подобных фактов. Все выявленные замечания устраняются. Без этого продукт из цеха не выйдет.
Качество готового продукта оценивается опытными специалистами-контролерами на финальной приемке, после чего происходит предъявление инспектору «Инспекторского центра вагонов и комплектующих», представляющему интересы РЖД.
Выпуск инновационной продукции традиционно сталкивается с различными преградами, в том числе и в области государственного регулирования. Как ОВК решает эту проблему?
Наши предприятия сертифицированы в соответствии с европейским стандартом менеджмента качества IRIS (International Railway Industry Standard). Основой для этого документа стала сложившаяся система управления качеством ведущих европейских производителей железнодорожной техники. Подобный системный подход позволяет нам выходить на рынки других стран, где высокое качество продукции и соответствие международным стандартам – наше конкурентное преимущество. Кроме того, выпуская продукцию нового поколения, мы, безусловно, привлекаем внимание сферы технического регулирования России, с тем чтобы они актуализировали нормативную базу, закладывали современные нормы и правила, которые бы позволяли выпускать все более совершенные образцы подвижного состава. Сами понимаете, что процесс этот не быстрый, требует значительных интеллектуальных и временных затрат. Наша компания стремится быть лидером и в разработке современных требований к продукту.
В компании внедряется система «Сокол», в которую вносятся все данные входного контроля. |
Как бы Вы в целом оценили систему управления качеством, созданную в ОВК?
Как специалист, знакомый со многими известными и лидирующими в своем сегменте предприятиями, могу с уверенностью сказать, что в ОВК система контроля качества одна из лучших, реально действующих в крупном бизнесе. Это касается и инструментальной, методической стороны, квалификации и мотивации персонала. Система контроля качества непрерывно совершенствуется, чтобы гарантировать соответствие продукции требованиям безопасности, надежности и эксплуатационного комфорта. Хочется отметить, что внимание, которое уделяется этому вопросу в нашей компании, и те инвестиции, которые тратятся на поддержание и совершенствование качественных характеристик продукции, – это стратегия лидера.
Зарубежный опыт
Лидеры глобального рынка транспортного машиностроения традиционно уделяют большое внимание качеству продукции. Во всех крупных компаниях заводы сертифицированы по стандарту IRIS. Он был разработан Европейской ассоциацией железнодорожной промышленности (UNIFE) в 2005 году. Главной целью IRIS является построение системы, позволяющей эффективно управлять качеством и безопасностью процессов при взаимодействии независимых бизнес-единиц. Для этого, в частности, реализуются принципы процессного подхода на всех этапах жизненного цикла продукции, внедряются нацеленные на непрерывные улучшения управленческие решения.
В настоящее время IRIS получили свыше 1,2 тыс. предприятий, еще 2 тыс. официально начали процесс сертификации (речь как о производителях техники, так и о работающих с ними поставщиках). Первый сертификат IRIS был выдан в июле 2006 года заводу компании Alstom в Орнане (Франция), для чего его сотрудникам пришлось ответить на 250 комплексных запросов аудиторов. Сейчас Alstom применяет разнообразный инструментарий контроля качества, в том числе активно внедряя методики систем бережливого производства. Это, например, следующие решения: 8D (системное устранение проблем), «пока-екэ» (снижение числа ошибок персонала), QRQC (быстрое реагирование службы качества).
Siemens придерживается схожих подходов, а кроме того, разрабатывает собственные автоматизированные системы контроля качества. На заводах компании используют программное обеспечение на основе платформы PLM (Product Lifecycle Management, управление жизненным циклом продукта) – САРА (Corrective and Preventive Actions, корректирующие и предупредительные меры). Оно позволяет систематизировать и анализировать информацию о сбоях и дефектах на любых участках и принимать своевременные решения по устранению проблем.
Компания Bombardier в дополнение к обязательному условию к своим партнерам о сертификации IRIS разработала Кодекс поведения поставщика. Документ, помимо условия вести ответственный бизнес (требования по охране окружающей среды, противодействию коррупции и т.п.), содержит добровольное согласие допускать представителей Bombardier или уполномоченных аудиторов для инспекций. Таким образом, компания на регулярной основе проверяет системы контроля качества своих контрагентов.
Владимир Змеющенко
Глоссарий: метод QRQC (Quick Response Quality Control)
Метод QRQC (Quick Response Quality Control), вероятно, является одним из самых мощных инструментов, доступных для быстрого и постоянного решения проблем качества, возникающих на низовом уровне.
В отличие от других инструментов для решения проблем, таких как 8D, DMAIC или 5W1H, , метод QRQC предлагает прагматический подход, направленный на устранение некачественного качества в кратчайшие сроки, непосредственно в том месте, где оно было обнаружено . Этот метод, в первую очередь, основан на объективном измерении и действует таким образом, чтобы предотвратить повторение проблемы.Давайте посмотрим на эту очень популярную методологию.
Шесть ключевых моментов метода быстрого реагирования на качество
Хотя истоки метода QRQC иногда приписывают производственной системе Toyota, изложенной Тайити Оно, и вытекающим из этого практикам бережливого управления, на самом деле он применялся в 1990-х гг. японская фирма Nissan. Его цели очень ясны и не могут быть более прагматичными:
- Всегда отправлять клиентам товары, соответствующие требованиям,
- Искоренять повторяющиеся инциденты,
- Повышать производительность,
- Сделать команды подотчетными.
Для достижения этих целей система Quick Response Quality Control основана в первую очередь на фактах. Не предположения, не гипотезы; этот метод основан на прямом, осязаемом наблюдении лиц, непосредственно вовлеченных в то место, где возникает проблема. Напротив, хотя предназначен для использования в производственных помещениях, он также служит для решения проблем в долгосрочной перспективе на шести ключевых этапах. :
- Идите туда, где возникает проблема, и понаблюдайте за ней.
- Изучите все детали, плохие и хорошие, а также выходные данные, чтобы точно понять, откуда взялась проблема.
- Общайтесь с людьми, используя только факты и реальные данные.
- Оперативное реагирование на конечного потребителя.
- Будьте логичны и основывайтесь на фактах, чтобы найти настоящие коренные причины проблемы.
- Объяснять другим людям и собирать отзывы, чтобы учиться на практике.
Следовательно, метод QRQC улучшает самоконтроль и усиливает подход к обеспечению качества на каждом этапе процесса. Хотя все сотрудники задействованы, менеджер берет на себя полную ответственность за метод, а также должен обеспечивать удовлетворение конечных потребителей. Менеджер обучает и направляет сотрудников в образ мышления QRQC, чтобы полностью внедрить его в культуру таким образом, чтобы каждый рассматривал проблемы как возможности для улучшения, начиная с этого момента .
Метод QRQC: метод управления, основанный на эскалации
Чтобы гарантировать быструю реакцию, дается крайний срок для предоставления ответа на проблему.По прошествии крайнего срока, если не было предоставлено жизнеспособного ответа, проблема передается на следующий уровень линейного управления, который, в свою очередь, должен соблюдать крайний срок, и так далее.
Этот фундаментальный принцип означает, что правильный уровень организации вовлечен в решение проблемы и, следовательно, в процесс постоянного улучшения. Эскалация напрямую связана со сложностью проблемы. Чем больше нерешенная проблема влечет за собой кросс-функциональные причины или чем больше людей требуется для ее устранения, тем быстрее происходит эскалация.То же самое относится к бюджету и ресурсам, выделяемым на меры по исправлению положения; чем они больше, тем выше разрешение.
На что нужно обратить внимание, чтобы добиться успеха?
Ускоряя взаимодействие между руководством и оперативным персоналом в случае возникновения проблем, метод QRQC показал, что он может дать значительные результаты. Фактически, можно сэкономить много времени на решении проблем, просто вовлекая сотрудников и возлагая на них ответственность. Вдобавок, помимо операционного персонала, поддержку могут также оказать вспомогательные и межфункциональные области, и, следовательно, операционное превосходство может процветать в любом бизнесе.
Тем не менее, есть некоторые моменты, на которые следует обратить внимание, если необходимо использовать всю эффективность метода QRQC:
- Не недооценивайте необходимую рабочую нагрузку – метод QRQC требует времени и энергии для всех сотрудников, чтобы освоить его. .
- Процедура должна быть организована и проводиться таким образом, чтобы все заинтересованные стороны были вовлечены в долгосрочную перспективу.
- Сосредоточьтесь на человеческом аспекте, а не только на производстве; метод дает результаты только в том случае, если все заинтересованные стороны должным образом задействованы.
- Получите представление обо всей экосистеме, чтобы убедиться, что все, кто вовлечен в проблему, вовлечены в решение, включая внешние стороны, такие как поставщики.
Чтобы узнать о передовых методах реализации успешных планов действий, незамедлительно загрузите нашу электронную книгу:
Контроль качества быстрого реагирования Nissan (QRQC) – Блог Мишеля Бодена
Система быстрого реагирования Nissan Quality Control (QRQC) – это управленческий подход. Речь идет об организации реагирования на проблемы с качеством, а не о технических средствах, используемых для их решения.Он предназначен для выявления проблем, их решения и документирования решений, тем самым повышая квалификацию сотрудников. QRQC не требует и не исключает средства защиты от ошибок или каких-либо инструментов статистики / анализа данных.
Это предназначено для ознакомления с QRQC тем, кто о нем не слышал, но это также призыв к практикующим исправить любые неправильные представления, добавить детали или поделиться своим опытом.
Lean, TPS и QRQC
QRQC не рассматривается ни в Справочнике Джурана по контролю качества, ни в инструментах Lean Toolbox Джона Бичено, ни в каких-либо публикациях Института бережливого предпринимательства.Это не часть производственной системы Toyota. На самом деле он возник в Nissan и распространился на автомобильную и аэрокосмическую промышленность Франции. На японском языке Nissan Production Way (NPW) (日 産 生産 方式, 2005) перечисляет его среди «25 ключевых слов» и посвящает ему четыре страницы. На французском языке “Набор инструментов бережливого производства” Раду Деметреску (La Boîte à Outils du Lean) имеет разворот на две страницы. Идеальный QRQC, Vol. 1 и 2, H. Audia et al. – единственные книги, посвященные QRQC на Amazon.
Происхождение и распространение
Казуо Кавасима считается изобретателем QRQC.Первоначально инженер-конструктор компании Nissan, он перешел на производство на заводе Nissan в Кюсю в 1993 году и отвечал за качество трансмиссии и сборки на четырех заводах Nissan в Мексике.
На заводе в Кюсю Кавасима заметил, что решение проблем с качеством откладывается из-за отсутствия однорангового сотрудничества на уровне организации, ближайшей к точке возникновения (POO). Организация находилась в разрозненном состоянии, и, например, чтобы получить инженерные ресурсы для решения проблемы в цеху, запрос руководителя группы шел вверх и вниз по иерархии, прежде чем его можно было утвердить.
Этот процесс не только потерял время, но и отфильтровал и исказил информацию до неузнаваемости к тому моменту, когда он мог с ней действовать. Его цель в QRQC заключалась в том, чтобы команды со всеми необходимыми навыками действовали автономно, как можно ближе к POO.
Усыновление в Valeo
В 2001 году Карлос Гон вернул Кавасиму в Японию, чтобы выбрать лучших поставщиков. Одним из поставщиков, которого он оценил, был французский производитель автозапчастей Valeo, который нанял его для внедрения QRQC в 2002 году.Valeo представила свой подход в этом видео 2017 года со своего завода в Анже:
Усыновление в Faurecia
Успех Кавасимы в Valeo привлек внимание других французских производителей автозапчастей. В 2006 году Faurecia наняла Киичиро (Кен) Сато, старшего вице-президента по качеству поставщиков в альянсе Renault-Nissan, для внедрения QRQC. Faurecia теперь называет это QRCI, что означает «Непрерывное улучшение с быстрым откликом», что предполагает более широкий диапазон, чем просто качество.В 2010 году Faurecia разместила следующее видео о внедрении QRQC на своем заводе в Henin-Beaumont:
Применение в аэрокосмической отрасли
Кавасима и Сато по-разному смотрели на QRQC и его реализацию. Однако оба были успешными в Valeo и Faurecia соответственно, что вызвало интерес к этому подходу в других отраслях, и в частности, в аэрокосмической отрасли в Groupe Safran.
ОднакоQRQC не был таким успешным в аэрокосмической отрасли, как в автомобилестроении, по причинам, которые открыты для предположений.Такая концепция, как время такта из немецкой авиационной промышленности, успешно перенесена в автомобилестроение в Японии, и, следовательно, возможно перекрестное опыление между этими отраслями.
Что такое QRQC?
Как поясняется в NPW, QRQC фокусируется на быстром реагировании на аномалии и дефекты, возникающие в производственном цехе. Это общий термин для системы, которая теперь нацелена как на качество , так и на другие проблемы . QRQC включает в себя как действия в реальном времени на производственной линии, так и более длительные циклы PDCA на посменной или ежедневной основе с участием инженеров и менеджеров.
В QRQC в реальном времени каждый производственный оператор обнаруживает аномалии и неисправности по мере их появления на каждой заготовке. Это механизм реагирования на месте в дополнение к контрольным точкам качества. Это также конструкция, предотвращающая выход дефектов ниже по потоку.
Ежедневный или посменный QRQC предназначен для системы управления, чтобы способствовать решению фундаментальных проблем на основе данных об аномалиях и сбоях, обнаруженных с помощью QRQC в реальном времени .
Цели QRQC
Цели QRQC аналогичны целям Toyota JKK:
- Для предотвращения перемещения дефектов по производственной линии. Не делайте браков и, если сделаете, не передавайте дальше! Разберитесь с этим на месте.
- Сделать проблемы видимыми и быстро их решить. В принципе, проблемы, обнаруженные с помощью QRQC в реальном времени , анализируются, и на следующий день принимаются контрмеры. Проблемы, которые технически требуют анализа, решаются за неделю.
- Сделать так, чтобы каждый оператор заботился о качестве и чтобы все производство было чутким и чутким к проблемам качества.
Область применения
NPW описывает QRQC как применимый к любой производственной линии с последовательностью операций. Однако актуальность дня или смены зависит от объема деятельности, которая имеет место в эти периоды. Если не остановить немедленно, станцию на конвейере сборки автомобилей с временем такта 60 секунд. который начинает выходить из строя, может вывести из строя сотни автомобилей за одну смену.Другое дело линия сборки самолетов с временем такта 3 дня, как и завод сборки компьютеров с временем такта 3 секунды.
Структура QRQC
QRQC направлен на решение каждой проблемы ближайшими к ней людьми на самом низком уровне иерархии управления. Для этого требуется структура и процесс эскалации от производственной линии до уровня команды или цеха и до уровня всего завода.
Ключевые точки реализации
Согласно NPW, первое, что нужно сделать, это убедиться, что операторы действительно останавливают линию, когда видят нарушение.Это предполагает предоставление операторам критериев для выявления отклонений и дефектов и способов сообщения о них на месте. Оператор нажимает кнопку остановки лески или тянет стопорный трос. Традиционно общение осуществлялось с помощью андонных огней и досок, а также музыки, ориентированной на местности. Сегодня вы можете подавать сигналы тревоги с помощью носимых устройств, таких как смартфоны или умные часы.
Отделы поддержки– инжиниринг, производственный контроль, обеспечение качества и техническое обслуживание – помогают, оперативно собирая и анализируя данные о POO, выявляя первопричины отклонений и дефектов, а также принимая немедленные контрмеры, визуализируя и обмениваясь информацией по мере необходимости для этой цели.
Следующая инфографика в переводе с NPW дает представление о работе QRQC:
Ежедневные процедуры QRQC
Предполагая, что на предприятии применяется QRQC в режиме реального времени, каждый производственный оператор или работник по контролю качества немедленно информирует руководителя о любом отклонении от нормы или дефекте и принимает меры на месте. Когда принять контрмеры слишком сложно, они следят за тем, чтобы следующая операция была уведомлена о необходимости корректирующих действий. Если это не так, при заключительной проверке появляется слишком много элементов для ежедневного анализа и выявления тенденций.Как только это произойдет, ежедневная активность QRQC будет выглядеть следующим образом:
- Ввод данных и обмен информацией . Окончательная проверка выявляет отклонения и дефекты, которые не удалось избежать в процессе производства и проверки качества, и вводит их в информационную систему в режиме реального времени для сообщения всем отделам.
- Подготовка встречи QRQC. Участники встречи QRQC решают, о чем докладывать на встрече, основываясь на разрезании данных, анализе и выявлении тенденций по всем операциям и окончательной проверке.
- T он QRQC Meeting . Руководители и сотрудники отделов поддержки встречаются каждое утро на 30-40 минут, чтобы (1) делиться новостями, включая вопросы, не относящиеся к качеству, (2) назначать ответственных за контрмеры, (3) отслеживать ход выполнения контрмер и (4) подтверждать их эффективность. Они подтверждают результаты по вчерашним проблемам и выдают инструкции на сегодня. Они документируют решения в таких формах, как «Лист ноу-хау по повышению качества» или «Лист отчета о состоянии» для совместного использования.
- Анализ и реализация контрмер. Следуя указаниям встречи QRQC, представители каждого отдела анализируют дефекты и разрабатывают меры противодействия. Для отклонений и дефектов, вызванных разработкой продукта или процесса, а не производственной линией, время выполнения заказа составляет неделю, чтобы определить меры противодействия.
- Обеспечение надежных контрмер . Вы включаете их в рабочие инструкции и при необходимости обновляете другие основные данные.
Красный ящик акцентирует внимание на дефектах: вы устанавливаете все станции, где вы проверяете качество, с красным ящиком или контейнером для дефектов. Это просто, но, очевидно, неприменимо к любому продукту, который не помещается в корзину. Следовательно, вы не можете использовать его для автомобилей или самолетов. Кроме того, он ограничивает цветовое кодирование, потому что вы не можете использовать красные контейнеры для каких-либо других целей.
В литературе QRQC также упоминается PDCA и «Три факта» (San Gen Shugi, 三 現 主義).PDCA – это общий план решения проблем. «Thee Actuals» – это альтернативная формулировка Genchi-Genbutsu Toyota. Это означает: идти туда, где это происходит, сосредотачиваться на реальности и иметь дело с реальными объектами. Это в отличие от обсуждения слайдов в конференц-зале. Однако обратите внимание, что инфографика NPW включает две сцены конференц-зала.
Описание задач отвечает на классические вопросы 5W1H – Кто, Что, Где, Когда, Почему, Как – с добавлением Сколько .Система полагается на формы, чтобы команды отвечали на все вопросы. Вопросы 5W1H – это то, на что журналисты учатся отвечать в начале каждой новости. С другой стороны, количество зависит от производства.
Описание не делает различий между немедленными контрмерами , такими как дополнительные проверки или тесты, которые предотвращают утечку дефектов, и решениями , которые устраняют основную причину проблемы. Если вы не можете решить проблему мгновенно, используйте немедленные контрмеры, чтобы продолжить работу, пока ищите первопричину.Инфографика NPW предполагает, что они на практике проводят это различие.
ПодходFord 8D к решению проблем действительно делает это различие, и он явно упоминается в реализациях QRQC за пределами Nissan. Буква «D» в 8D означает «дисциплина», а не «шаг», что предполагает, что они не являются строго последовательными, и их 9, а не 8:
- Подготовка и аварийное реагирование
- Создайте команду людей со знанием продуктов / процессов.
- Опишите проблему
- Разработать временный план содержания
- Определение и проверка основных причин и точек выхода
- Проверить постоянные исправления (ПК) для проблемы, которая решит проблему для клиента
- Определите и выполните корректирующие действия
- Предотвращение повторения / системные проблемы
- Поздравьте основных участников вашей команды
Участники QRQC документируют свою деятельность в формах и размещают их на информационных досках на всех задействованных уровнях управления.QRQC включает сбор и анализ данных, но не требует использования каких-либо конкретных инструментов для этой цели.
#qrqc, #nissan, #valeo, #faurecia, #lean, #tps, #npw, #tps, #leanquality, #quality, #qualityassurance
Нравится:
Нравится Загрузка …
QRQC: Quick Response Quality Control в Valeo
Недавно Мишель Боден написал на своем сайте краткое сообщение о Quick Response Quality Control или QRQC и разместил его также в LinkedIn. Тем самым он пригласил практикующих, в том числе и меня, внести свой вклад в знания о QRQC.Поскольку я чувствую, что краткий ответ на LinkedIn не отражает богатство QRQC, я решил посвятить сообщение этой теме. Однако без амбиций попытаться быть полным в этом посте, что, как мне кажется, невозможно с такой обширной темой, как QRQC. Но давайте погрузимся в подробности и поделимся некоторыми из моих впечатлений и взглядов на QRQC, как я пережил и прожил это в Valeo в то время.
QRQC: Мой опыт
Мой опыт работы с QRQC восходит к 2002 году. Я присоединился к Valeo через два месяца после того, как Кадзуо Кавасима присоединился к группе, в начале 2002 года.Присоединившись, мне предложили возможность посетить «школу Ичикох», где мы изучали, как Ichikoh использует QRQC, среди других элементов своей производственной системы. На картинке выше изображена команда, с которой я учился в школе Ичоко. Ичикох входил в состав компании Nissan Keiretsu, а Valeo уже имела финансовую долю в группе (тем временем полностью перешла к Valeo).
Встреча QRQC в Ичикох Исехара
В то время старшие менеджеры Valeo Lighting Systems (VLS) регулярно участвовали в серьезных ознакомительных поездках в Ичикох в Японии (известную как «Школа Итико»), в частности, с участием их предприятий в Исехара и Фудзиока.Только в 2002 году более 90 старших менеджеров VLS со всего мира приняли участие в различных сессиях школы Ichikoh. Благодаря этим отношениям с Итико Валео уже хорошо знал о QRQC, так как я видел, как QRQC документировали в рамках этих учебных поездок задолго до того, как Кавасима присоединился к Валео. Но по-настоящему они начали развиваться только после того, как к нам присоединился Кавасима.
По состоянию на середину 2002 года группа полностью приняла QRQC, и тогдашний генеральный директор Valeo Тьерри Морен заявил, что «культура Valeo будет основана на san gen shugi» и что «на каждом сайте необходимо применять QRQC».Как и почти все сотрудники Valeo, я был тщательно обучен QRQC, и в моей роли директора по цепочке поставок и логистике филиала «Системы освещения» также отвечал за развертывание его в рамках этой функции на его 17 заводах по всему миру, а также обучал различные команды их работе. усилия по решению проблем с использованием QRQC после его развертывания.
QRQC: философия, лежащая в основе QRQC
QRQC опирается на три основных элемента:
1. «Три Реала» или «Сан Ген Шуги».
2. Быстрое реагирование
3. Контроль
QRQC: Сан Ген Шуги
Во-первых, философия «Трех Реалов» или «Сан Ген Шуги» заставляет людей всегда думать о реальном месте и реальном времени («ген-ба»), реальной части («ген-буцу») и быть сосредоточен на реальности («ген-джитсу»). По моему опыту, эта философия определяет отношение и рефлексы организации. Это подразумевает многие вещи, которые с тех пор стали моими стандартными рефлексами при обучении людей и команд в процессе решения проблем.
Покойный Кавасима-сан всегда говорил: «У меня есть только два инструмента: мои глаза и мои ноги. Это все, что мне нужно увидеть, судить, рассмотреть, принять решение. Это основа «сан ген сюги». Именно это мышление лежит в основе всех методов решения проблем в QRQC. Вопрос: «Вы применили сан ген сюги?» Был в то время на всех наших подписях в электронной почте…
«Сан ген сюги» подразумевает, что вы должны рассматривать себя как детектива, работающего над расследованием преступления. Это означает, что вы немедленно отправляетесь на место фактического преступления (чтобы не потерять никаких улик), чтобы найти улики, исследовать механизм, с помощью которого возникла проблема, и поговорить с реальными свидетелями.Это также заставляет вас проверить действительно плохую часть и сравнить ее с действительно хорошей частью и соответствующими стандартами, а также установить несоответствие лично и из первых рук. И он фокусирует вас на реальности, на истинных фактах, на том, чтобы не гадать, искать доказательства, проверять факты и не предполагать. Трудно передать словами, что это значит, если вы действительно применяете это в своем коучинге, и когда менеджеры ежедневно бросают вызов своим командам. Он создает «кизуки»: способность замечать.
QRQC: Быстрый ответ
Второй фундаментальный элемент QRQC – это скорость. Быстрое реагирование подразумевает быстрое обнаружение проблемы, немедленное реагирование для защиты клиента и стандартные (и относительно короткие) сроки для устранения основной причины проблемы. Его философия заключалась в том, чтобы думать часами и днями, а не неделями.
Таким образом, помимо QRQC, направленного на устранение первопричин, у него также был сильный подход в первый момент и через несколько часов после обнаружения проблемы (кстати, оба после фазы PDCA).Он включал в себя такие практики, как «первая остановка дефекта», маркировка деталей, использование красных контейнеров / стоек / областей (связанных с процедурами управления на генба), определение характеристик проблем с использованием 5W1H (что интересно как с точки зрения производителя, так и с точки зрения клиента), проверка соответствия называемые диаграммами поиска и устранения неисправностей, и выполнение заранее определенных стандартных реакций. Обычно они включали в себя такие вещи, как сортировка всех последующих частей – что также является хорошим источником факторов, если все сделано правильно -, установка качественной стены и выполнение протоколов связи с клиентами.
Опять же, трудно передать, что это значит для культуры, но я могу сказать вам, что если вы верны этому элементу философии QRQC, в цехах будет постоянный шум; шум, который отличается от того, к чему вы, возможно, привыкли, как посетители в то время, – но также и некоторые недавние клиенты, которых я взял с собой для посещения сайтов Valeo, – сказали мне.
Я также до сих пор помню одну из сильных тренировок Кавасимы-сана в 2002 году, когда он, как известно, выбросил хорошо известный принцип Парето или анализа 80-20 в мусорное ведро; Вы бы сказали, что это все еще качественный 101 инструмент.Он объяснил по-своему (он был довольно сильной личностью, я могу сказать по опыту…), насколько мы были глупы, чтобы сначала собрать достаточно данных в течение достаточно длительного периода времени, чтобы иметь возможность составить такую диаграмму, и только затем приступайте к решению проблем. Дело было ясным.
QRQC: Контроль
Третий фундаментальный элемент называется «контроль». Контроль в QRQC подразумевает строгость и дисциплину как в логике нашего мышления, так и в выполнении метода (а также в следовании его правилам и с использованием установленных стандартов).Я до сих пор помню большие баннеры, которые висели в зонах QRQC, напоминая нам всеми заглавными буквами о необходимости применять «ЛОГИЧЕСКОЕ МЫШЛЕНИЕ».
Именно здесь вы должны выделить некоторые методы решения проблем, такие как анализ факторного дерева (FTA), который является расширенной и гораздо более строгой формой хорошо известной техники Исикавы, которая включала проверку фактической релевантности фактора на так называемая контрольная точка на генба, анализ 5x Почему и 3A. Рекомендую прочитать мои посты по этим темам.Эти методы не являются «ракетостроением» и не новы, но отличалось то, как они использовались: строго и с чрезвычайно сильным акцентом на верификацию и доказательства в цехах.
Сильным дополнением, которое я всегда находил, является то, что QRQC явно фокусируется как на проблеме возникновения (почему проблема возникла?), Так и на проблеме обнаружения (почему мы не обнаружили ее до того, как это произошло?). То, что G8D называет «точкой выхода». QRQC применяет всю свою строгость к обоим элементам задачи, конечно, применяя «сан ген сюги».
Для всех упомянутых шагов и методов использовались шаблоны, которые были включены в исчерпывающую форму QRQC, что заставляло группы по решению проблем быть дисциплинированными в их усилиях по решению проблем. Правда в том, что, как это часто бывает, на самом деле это также сильно зависело от команды, их менеджера и их возможного тренера. Вот почему формирование культуры и лидерства вокруг любого подхода всегда так важно. Только подумайте о том, как руководитель завода говорит команде, занимающейся решением проблем, воссоздать проблему, когда они «думают», что нашли первопричину…
Я также обнаружил, что реальная разница с другими подходами к решению проблем – это структура связи вокруг QRQC с ее линейным уровнем QRQC, совещанием QRQC отдела и последующим совещанием QRQC завода.Он включал стандарты и формы для регистрации проблем, определения проблем, частоты проверок и т. Д. все очень наглядно.
Контроль в QRQC также подразумевает дисциплину в реализации действий, исходящих от QRQC (вовремя и в соответствии с решением), и дисциплину в фактической проверке как их реализации, так и ее эффективности с течением времени и несколькими уровнями управления.
И контроль впоследствии означает, что эффективные меры противодействия применяются до тех пор, пока они не будут стандартизированы и полностью интегрированы в систему работы компании.Это означало, что последствия переводятся в обновленные (визуальные) процедуры, инструкции, обучение и сертификацию операторов, правила проектирования, спецификации, контрольные списки, FMEA и так далее.
QRQC: За пределами решения проблем
Следует знать, что QRQC в целом – это гораздо больше, чем просто метод решения проблем, на котором мы обычно сосредотачиваемся при обсуждении QRQC. Решение проблем упоминается как (только) этап 1 QRQC.
QRQC в целом также включает в себя больше: он включает в себя предотвращение проблем с помощью Yokoten, стандартизацию, такую далеко идущую, как дизайн продукта, и обучение на рабочем месте по кайдзен, и это лишь некоторые из них.И все эти последующие шаги QRQC также, опять же, включали несколько методов и шаблонов, например, такие как карта извлеченных уроков (LLC). Более чем один пост может охватить.
Я уверен, что этот пост не может передать реальное влияние такой практики, как QRQC, если все сделано правильно. Но я надеюсь, что этот пост дает вам, по крайней мере, несколько лучшее понимание и ощущение того, что может означать для компании сила подробного, строгого и всеобъемлющего подхода к решению проблем, заложенного в философии «сан ген сюги».Это позволило Valeo выиграть премию Toyota Supplier Quality Award и сократить количество дефектов до однозначных значений ppm; даже вызвав обсуждения на некоторых заводах, возможно, изменить шкалу ppm на ppb-one…
Для тех, кто хотел бы узнать больше о QRQC, я рекомендую книги Хакима Аудиа и Квинтина Теста по QRQC, которые в значительной степени описывают технический подход, используемый в Valeo (а затем и в Faiveley Transport). А для тех, кто искренне хочет испытать QRQC: найдите себе опытного тренера.
Тренинг QRQC – развитие компетенции управленческих команд
1. Система менеджмента качества:
- Методы идентификации рисков в процессе
- Lean Management – определение инструментов непрерывного улучшения
2. QRQC – создание группы управления производством
- Quick Response Quality Control – метод быстрого реагирования на сбои
- Специфика задач и ответственности в команде
- командная организация, коммуникация, отчетность, эскалация
3.Решение проблем качества на производственной линии:
- QR – быстрое реагирование на ошибки: обсуждение действий, которые необходимо предпринять в случае, например, жалобы, изменения в процессе или событии (немедленные действия – 24 часа) вместе с определением ответственности и проверкой выполненных действий и их эффективности
- 3R – San Gen Shugi, цикл PDCA вместе с объяснением методов с практическими примерами использования в производственной сфере.
- GEMBA – перейдите к месту, где возникла проблема
- GENBUTSU – анализ деталей
- GENJITSU – работа с данными
- Вовлечение групп QRQC для выполнения анализа непосредственно на производственной линии – устранение уверенности в том, что мы знаем производственную зону без проверки на месте происшествия
- Красный ящик – это не только физическое место, куда мы помещаем детали, не соответствующие спецификации в процессе, но и поддержка команд QRQC, которую могут предоставить менеджеры.
- Представляем, как решать проблемы с истекшими сроками
- AQM – матрица авто качества
Инструмент для команд QRQC, на основе которого мы можем анализировать не только причины проблем, но и оценивать уровень обнаружения и реагирования на ошибки в процессе.
- AQM представляет собой метод, который можно использовать в ситуациях повышенной текучести кадров, Quality Wall начальный этап и в ситуации, когда компания анализирует возможность снижения контрольной частоты (устранение MUDA )
- Обучение на рабочем месте (OJT) :
- Метод наблюдения за командной работой на каждом уровне организации.Это позволяет руководителю работать напрямую с командой, чтобы повысить эффективность работы, проанализировать качество и исключить повторение (возникшая проблема).
- Представление бланка, способы выполнения OJT
4. Решение проблем – FTA PDCA
- QR – идентификация проблемы ( 5W2H )
- Меры немедленного реагирования
- Сортировочная организация и выводы
- Назначение – ускорение процесса
- Анализ FTA – потенциальная причина выявления ошибки
- Анализ FTA – потенциальная причина отсутствия ошибок при обнаружении
- 5Whys – определение первопричины
- Воспроизведение дефекта
- Допуск к устранению неисправностей
- Проверка эффективности деятельности
5. Карточка усвоенных уроков – результаты анализа
- Учимся на ошибках
- Стандартизация деятельности
(PDF) Контроль качества быстрого реагирования как инновационный подход в условиях железнодорожного транспорта
2
Сеть конференций MATEC 183, 03003 (2018) https://doi.org/10.1051/matecconf/201818303003
QPI 2018
Адаптация к изменениям – это не вариант, а требование, если железная дорога хочет выжить и
процветать.Во всем мире существует несколько известных подходов к управлению качеством, и
в соответствии с требованиями транспортного рынка очень важно применять их на
новых подходах. Возникло влияние рынка, бросившее вызов статус-кво, включая различные подходы
Джурана, Деминга или других известных участников тотального контроля качества. Необходимо связать
стоимости мониторинга качества с ориентацией на потребителя, с
– ориентацией на процесс в области качества [3].
Существуют типичные видимые характеристики для развития железнодорожного рынка в связи с управлением качеством
, такие как либерализация транспортного рынка и особые условия в продукте
, обеспечивающем взаимосвязь потребностей клиентов. Конкретная цель перевозки –
, поэтому удовлетворяет потребность в мобильности как в пассажирском, так и в грузовом транспорте [4].
2 Необходимый инновационный подход к управлению качеством на железнодорожном транспорте
грузовые перевозки
Железнодорожные грузовые перевозчики стремятся создать такие условия для своих клиентов, чтобы
поддерживал существующие перевозки и получал новые транспортные заказы.Например, государственная железная дорога
, грузовой перевозчик в Словакии, объемы перевозок во многом зависели от ситуации
и развития металлургической промышленности в Словакии и соседних странах. На долю металлургии
приходится до 66% от общего объема перевезенных грузов
. Также происходят большие изменения в деловых отношениях металлургических заводов
или их производства, когда потоки транспортировки товаров изменяются или перемещаемый товар
изменяется, что, следовательно, связано с изменяющимися требованиями
к использованию локомотивов. или типы вагонов для перевалки [5].
Железнодорожный грузовой транспорт создает сложную систему, в которой существует множество воздействий, но новая проблема
для него характеризуется поиском прогрессивного маршрута для обхода некачественных услуг.
Качество услуг по железнодорожным грузовым перевозкам можно отслеживать в рамках всей транспортной цепочки
или в отдельных ее этапах. Актуальной задачей является определение качества
не только до или во время перевозки, но и после нее.При этом
клиенту часто требуются дополнительные услуги, в конце концов, если клиент
не доволен транспортировкой, он предъявляет претензию. Предприятиям, занимающимся железнодорожными грузовыми перевозками, необходимо найти
соответствующих ответов на проблемы и защитить своих клиентов [6].
3 Применение быстрого контроля качества при железнодорожных грузоперевозках
транспорт
Эта философия подчеркивает командный подход и заключается в быстром реагировании на накопившуюся проблему
и необходимости защиты клиента и процессов, прежде чем оставаться в нежелательной
ситуация.Этот метод универсален, и каждое железнодорожное предприятие может немного модифицировать его для конкретных транспортных процессов. Одновременно с этим необходимо
постоянно отслеживать процессы и решать конкретные задачи на основе текущих тенденций и, таким образом,
оперативно управлять внутренними процессами на железнодорожном транспорте. QRQC основан на
действиях, таких как первоначальное обнаружение проблемы, коммуникация и распределение
проблемы на всех уровнях в рамках процессов железнодорожного транспорта, от сотрудников первого контакта до
и до менеджеров высокого уровня.После анализа и определения решения проблемы приходит
сама проверка, которая определяет, было ли выбранное решение правильным и был ли достигнут желаемый результат
.
Рис. 1. QRQC в условиях железнодорожного предприятия.
Это позволяет четко определить важные факторы, вызывающие проблемы в различных областях
, таких как логистика, транспортные операции и транспортные услуги с соответствующим качеством.Что касается железнодорожных перевозок
, этот упомянутый подход к качеству был применен Жилинским университетом в рамках сотрудничества
с государственной железнодорожной компанией Cargo Slovakia, a.s. (ЗССК ГРУЗ). Это исследование
было проведено в отношении применения этого метода в случае сертифицированного продукта
«логистические поезда». Этот тип продукта подходит для клиентов, которые используют метод логистики
как раз вовремя, этим поездам уделяется больше внимания, а в добавлении
считаются приоритетными.Железнодорожная компания ZSSK CARGO имеет
внедренную систему менеджмента качества для этих поездов, а также имеет сертификат качества ISO 9001: 2009
. Исследования показали следующие преимущества:
• анализ, который необходимо провести в случае возникновения проблемной ситуации в процессе,
• заранее организованная и работающая команда, регулярно встречающаяся по этому продукту,
• сбор данных проблема в процессе в нужное время и немедленно сообщая о проблеме
, а затем создавая последующую документацию,
• внедрение постоянного подхода к решению проблемы с помощью трудолюбивой команды
,
• способность предотвращать проблемы путем сосредоточения по внутренним процессам.
Начальник отдела железнодорожной компании должен понимать принципы QRQC, чтобы
смог устранить растущую проблему и понять основные трудности в рамках
транспортных процессов [7]. Последовательность шагов проиллюстрирована на следующем рисунке.
9782840017103: Perfect QRQC (Quick Response Quality Control) (французское издание) – AbeBooks
Недавние проблемы с качеством привели к отзыву многих продуктов в автомобильной, пищевой и фармацевтической отраслях.
.Последствия часто бывают драматичными, как с человеческой, так и с финансовой точки зрения.
QRQC (Quick Response Quality Control) – крупная инновация в области управления качеством. Это
, сочетающий в себе управление и подход для простого и логичного решения большинства производственных и функциональных проблем.
Valeo, один из ведущих мировых поставщиков оборудования, использует QRQC более 10 лет. QRQC имел
, что позволило Valeo Group изменить шкалу измерения качества с PPM (частей на миллион) на PPB
(частей на миллиард).
Подход QRQC опирается на два столпа:
Отношение Сан Ген Шуги, основанное на 3 реальных принципах, направленных на то, чтобы попасть в реальное место (Генба),
с реальными частями (Ген-бусту) и реальными данными / фактами. (Gen-jitsu)
Управленческая деятельность, состоящая из 4 этапов: обнаружение, коммуникация, анализ и проверка
Хаким Аудиа и Квинтин Теста, ведущие эксперты QRQC и директора по качеству в Valeo, объясняют в этой первой книге
основы QRQC по порядку. для создания программы Robust Design.Они подробно описывают, как
успешно внедрить принципы QRQC, чтобы получить как немедленную, так и долгосрочную выгоду.
“синопсис” может принадлежать другой редакции этого названия.
В.R.Q.C Контроль качества быстрого реагирования
Презентация на тему: «Q.R.Q.C Quick Response Quality Control» – стенограмма презентации:
1 Q.R.Q.C Контроль качества быстрого реагирования
M Davies – август 2009 г.
2 (Быстрый контроль качества) НЕТ ВООБРАЖЕНИЯ, ТОЛЬКО ФАКТЫ.
ЧТО ТАКОЕ QRQC? (Быстрый контроль качества) QRQC основан на “Сан Ген Шуги”. Сан Ген Шуги – это японское выражение, означающее «три реальности»: Ген-ба: реальное место Ген-буцу: реальная часть Ген-джитсу: реальность Применяйте принципы QRQC в полевых условиях каждый день и извлекая уроки из опыта работы в полевых условиях. : НЕТ ВООБРАЖЕНИЯ, ТОЛЬКО ФАКТЫ.
3 Активность на основе данных на основе голоса клиента
Q.R.Q.C Methodolgy Деятельность, управляемая данными, основанная на голосе клиента Голос процесса
4 КАК РАБОТАЕТ QRQC? Многоквалифицированные команды (QA / Eng. / Prod. / Logistics)
Ежедневные встречи для оценки проблем (сбор данных) Целевые инструменты качества 3 основных проблем, используемые для исследования первопричин проблем Члены группы, которым поручено выполнение действий Время выполнения агрессивных задач (СЕГОДНЯ! !!!операторы
5 ЦЕЛЬ не СУБЪЕКТИВНАЯ
QRQC в действии Первым шагом в QRQC является согласование СТАНДАРТОВ Стандарты, согласованные с заказчиком, или установление внутренних стандартов делают ЦЕЛЬ контроля качества не СУБЪЕКТИВНОЙ
6 QRQC в действии Второй шаг в QRQC – обеспечение ОТСЛЕЖИВАНИЯ
Отслеживание до смены, оператора и времени производства Это позволит выделить любые события особой причины
7 QRQC в действии Решение, основанное на данных
Третий шаг в QRQC – это «Мониторинг и сбор данных». Для любого анализа первопричин должны использоваться точные и текущие данные. Используйте основные инструменты 8D для решения проблем, которые будут использоваться для анализа основных причин. Два типа отказов – сбой процесса. – Как дефект привел к провалу проверки – Почему не обнаружено решение, основанное на данных
8 ЧЕЛОВЕК НА РАБОТЕ ЛУЧШЕ ЗНАЕТ ПРОЦЕСС
QRQC в действии Четвертый этап QRQC – ОБРАТНАЯ СВЯЗЬ Обратная связь с операторами по всем вопросам Визуальное управление ЧЕЛОВЕК НА РАБОТЕ ЗНАЕТ ЛУЧШЕЕ ПРОЦЕСС
9 Дисплей хорошо виден для всех
QRQC в действии Пятый шаг в QRQC – УЛУЧШЕНИЕ ПРОЦЕССА Любые внесенные улучшения должны быть выделены для всех, а любая документация по контролю процесса обновлена любыми новыми параметрами (храповое устройство для удержания прироста) E .